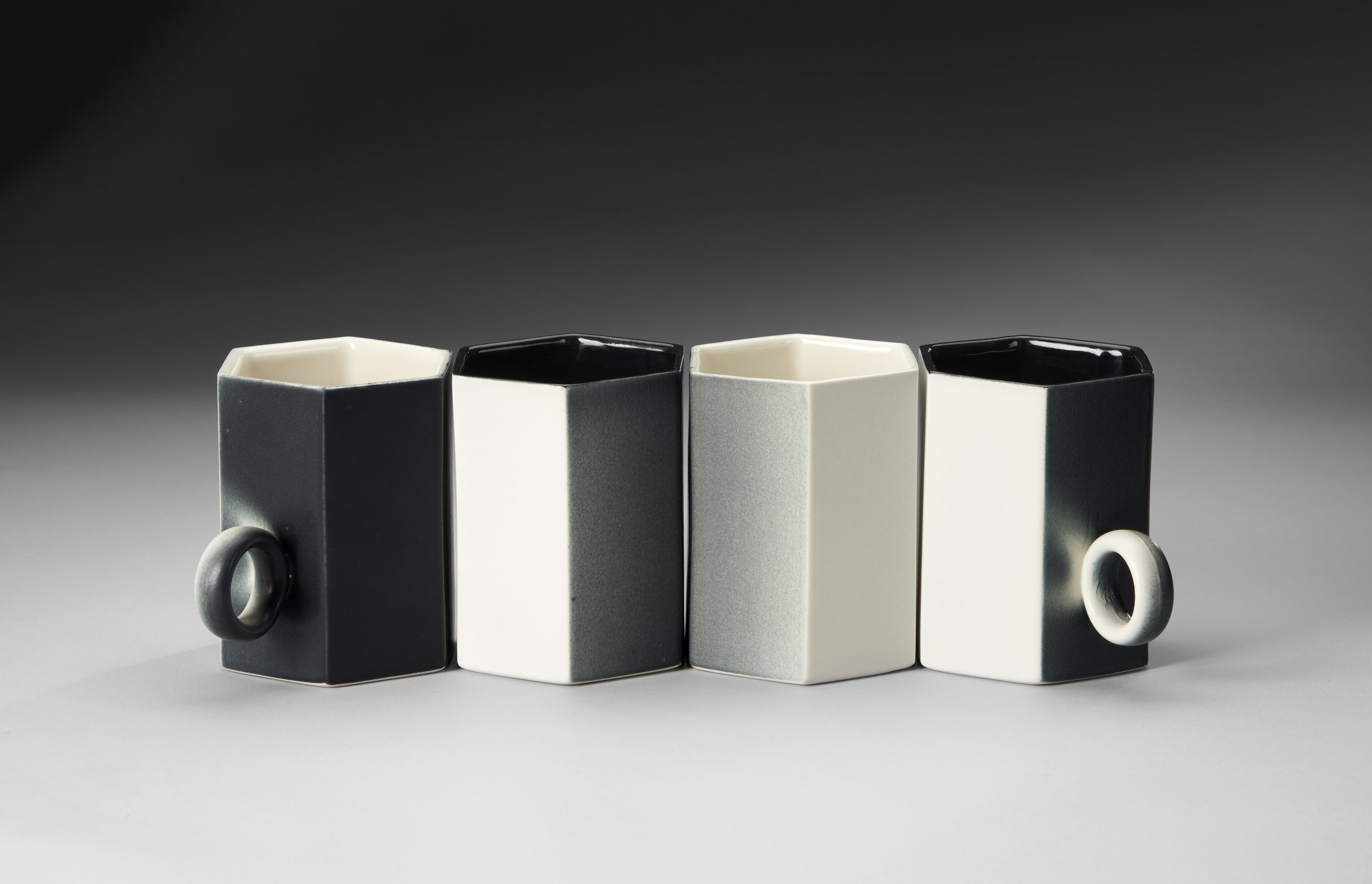
Windgate-Lamar Grant Recipient, April 2023
Awarded by the Center for Craft
Windgate-Lamar Fellowship
Each year, the Windgate-Lamar Fellowship identifies ten undergraduate graduating college students with exemplary skill in craft. Awardees receive $15,000 - one of the largest awards offered nationally to art students.
Final Portfolio
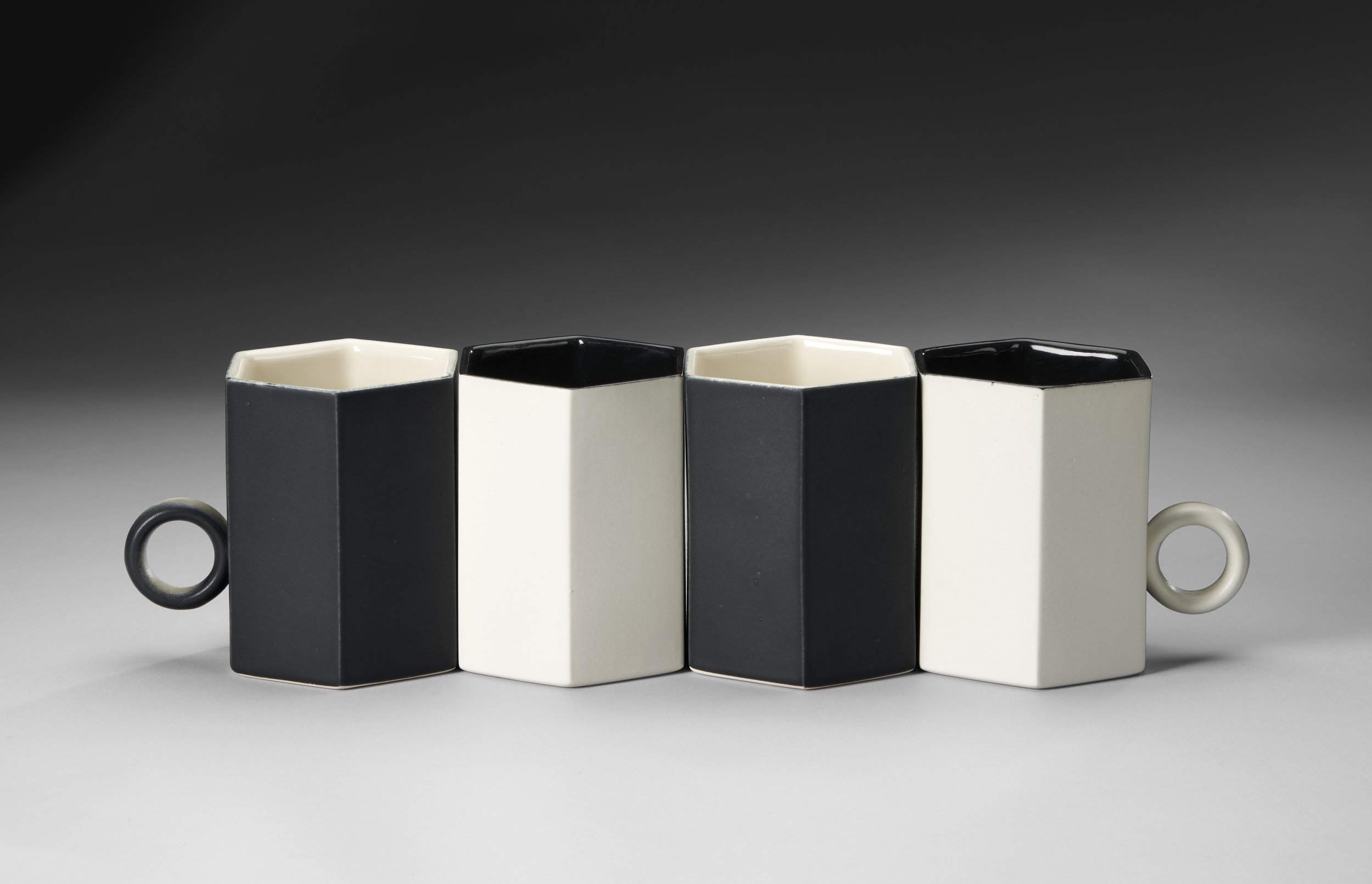

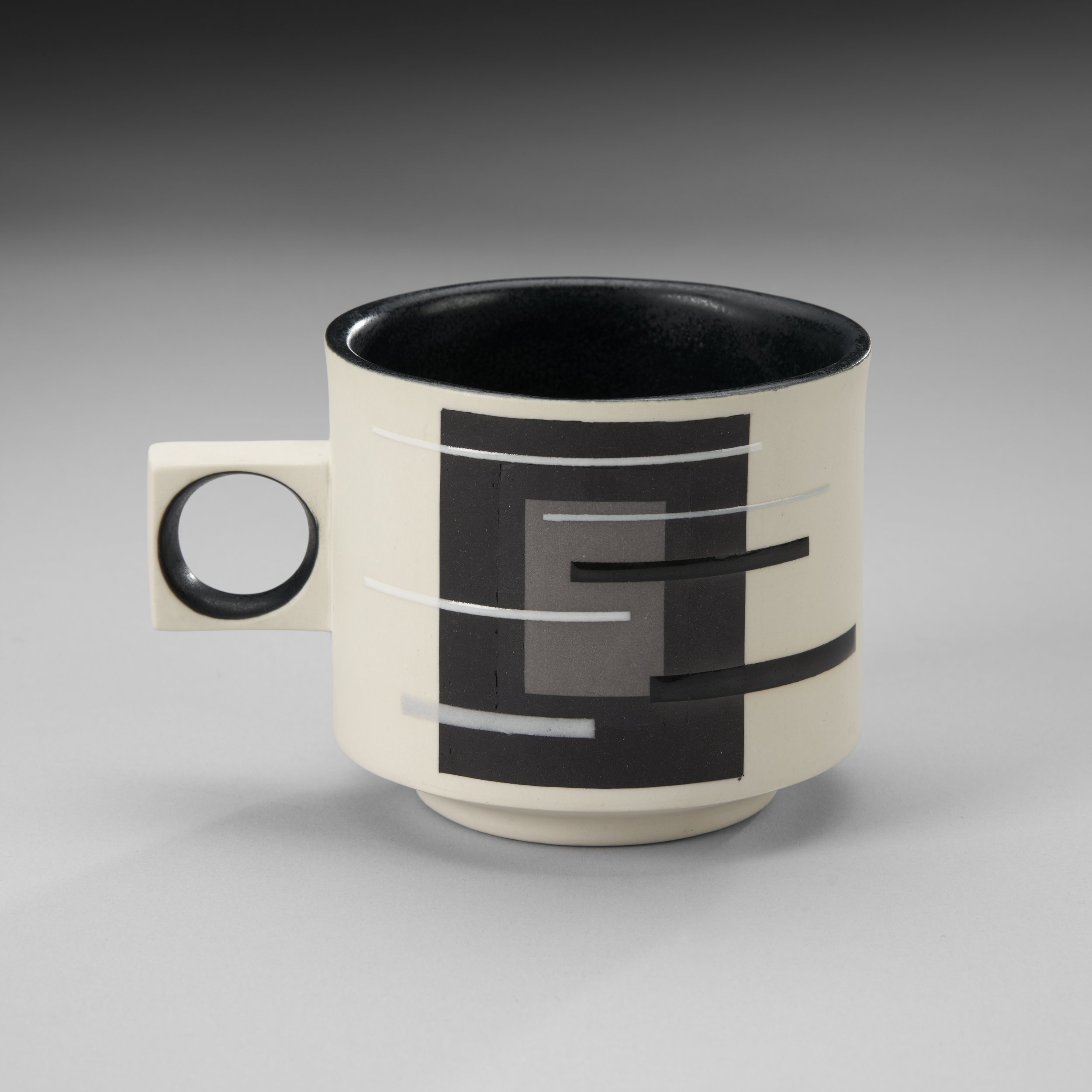
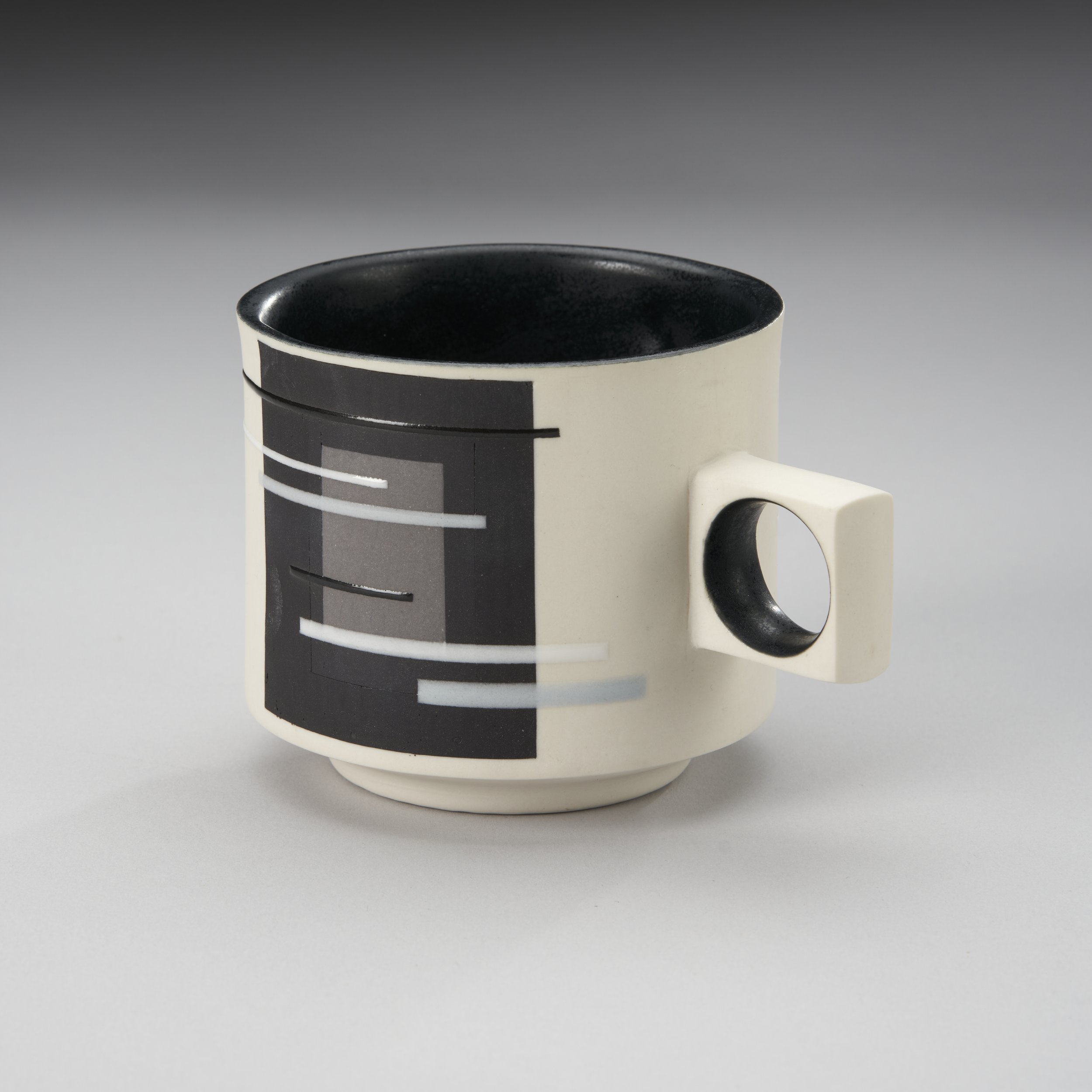
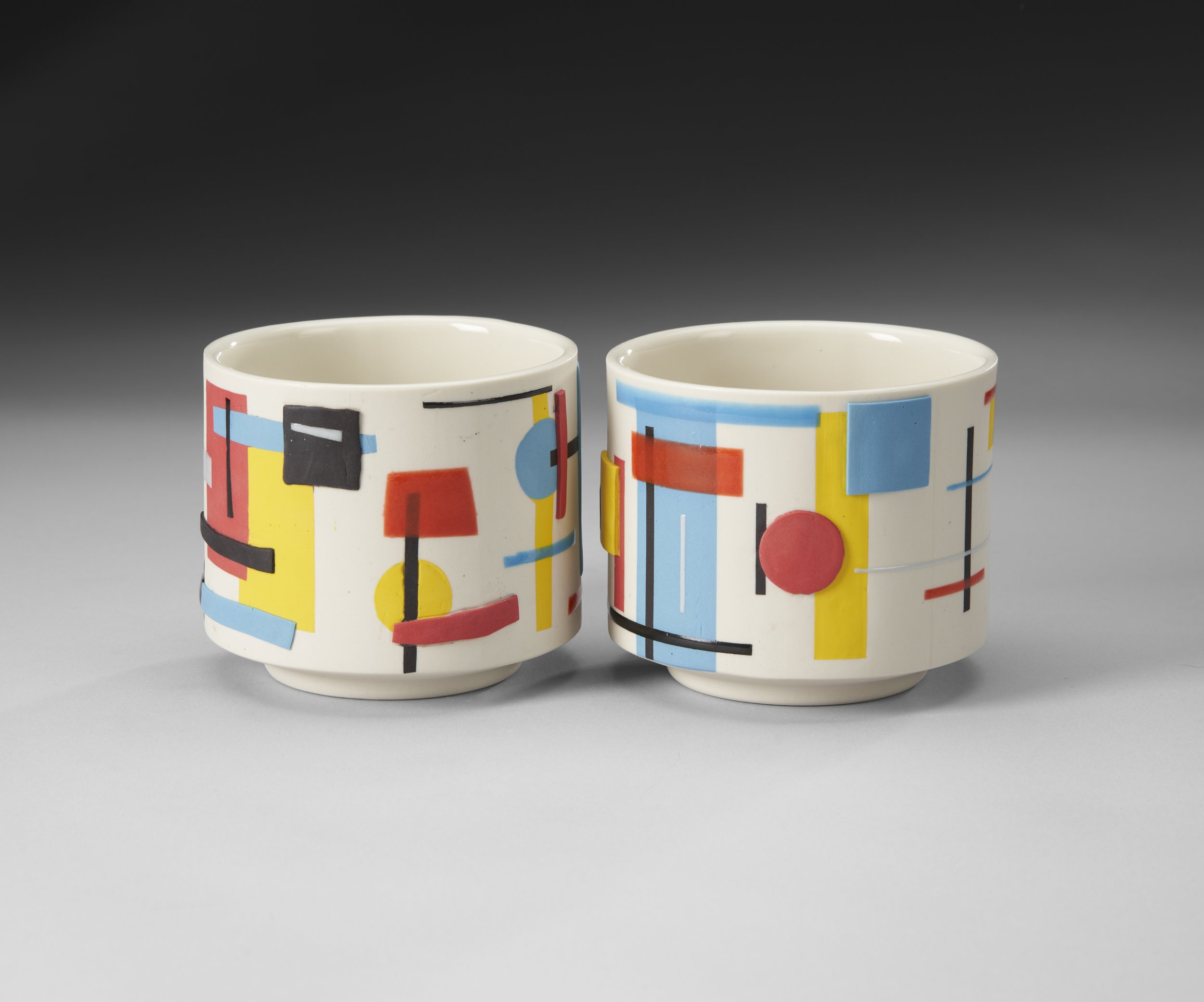
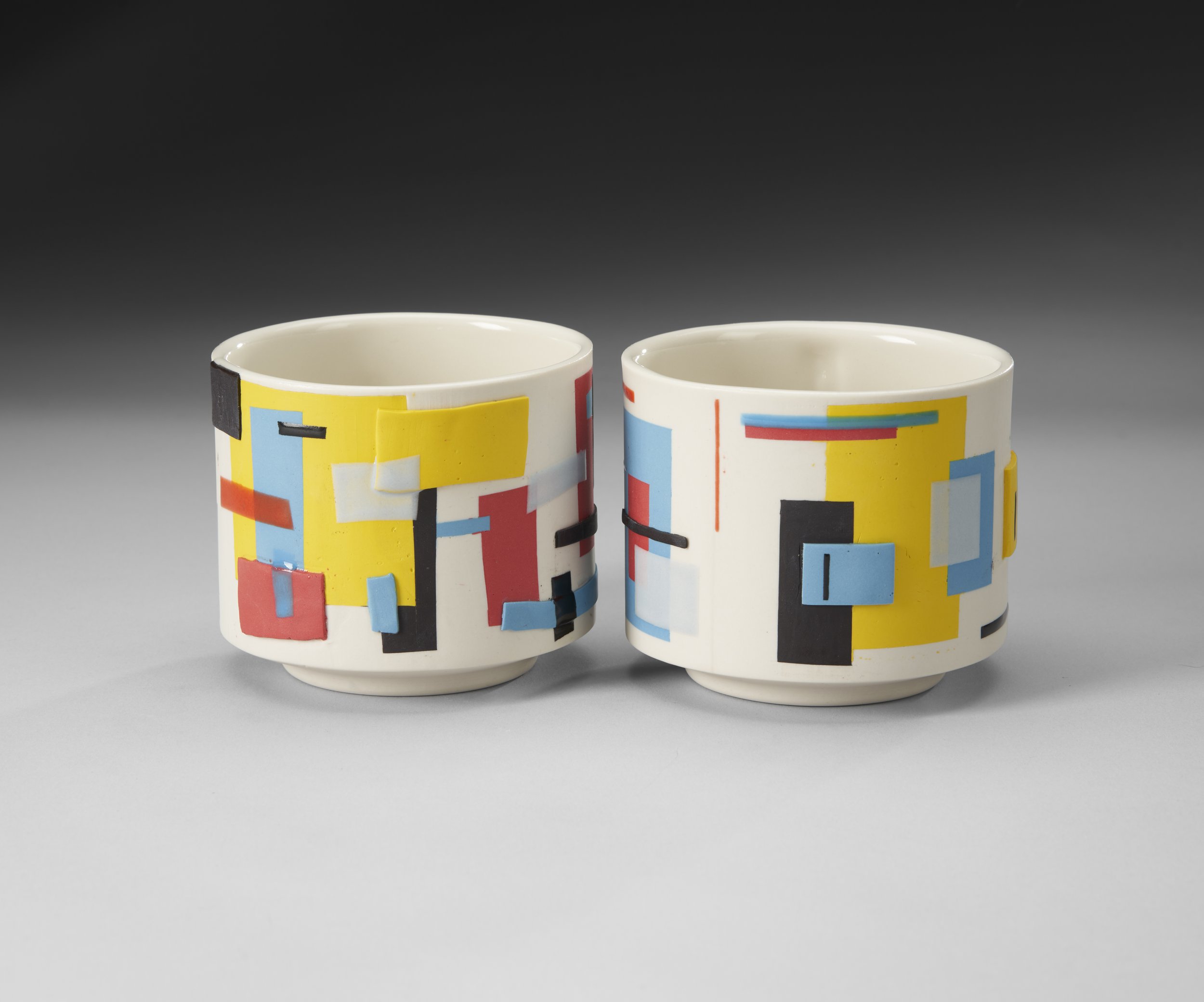
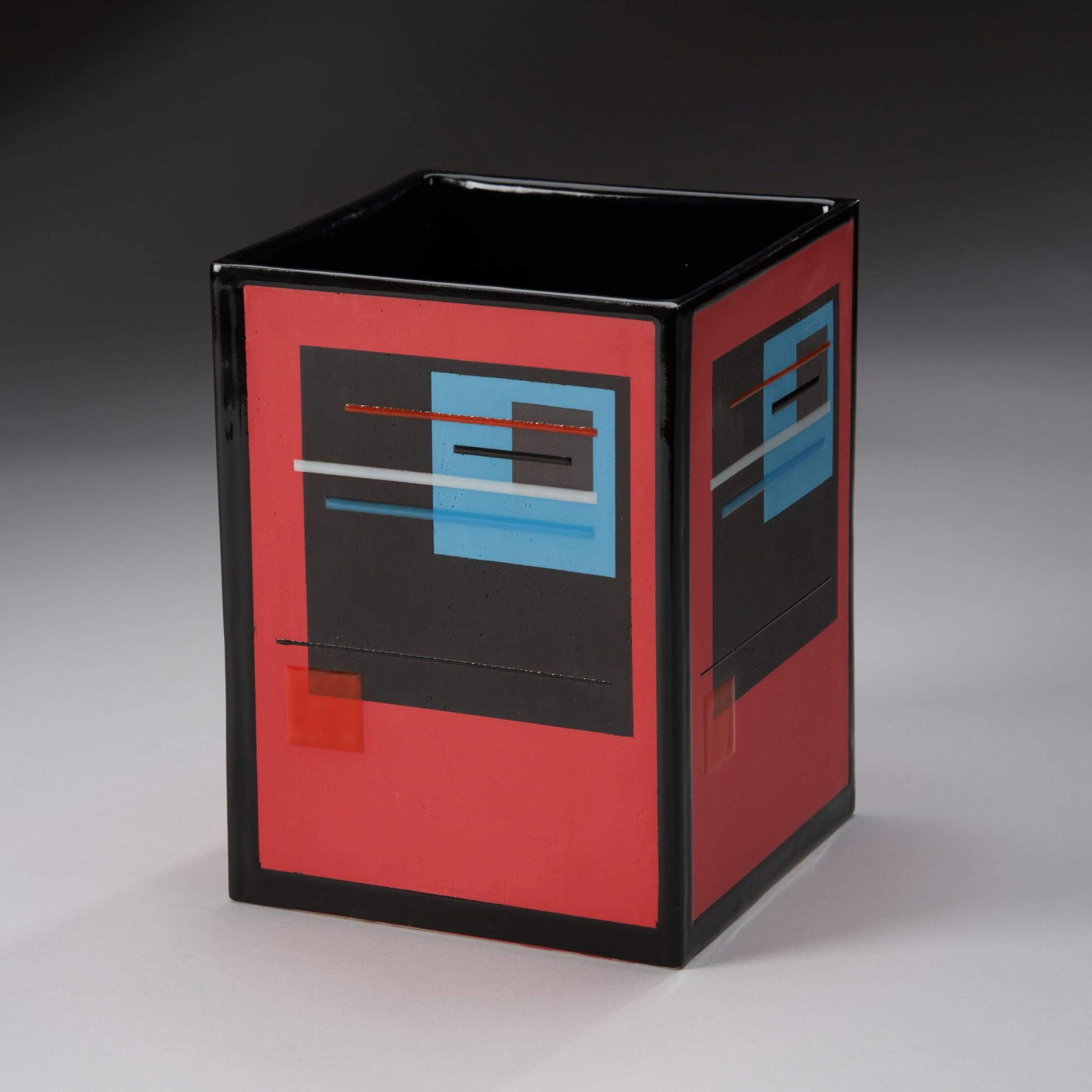
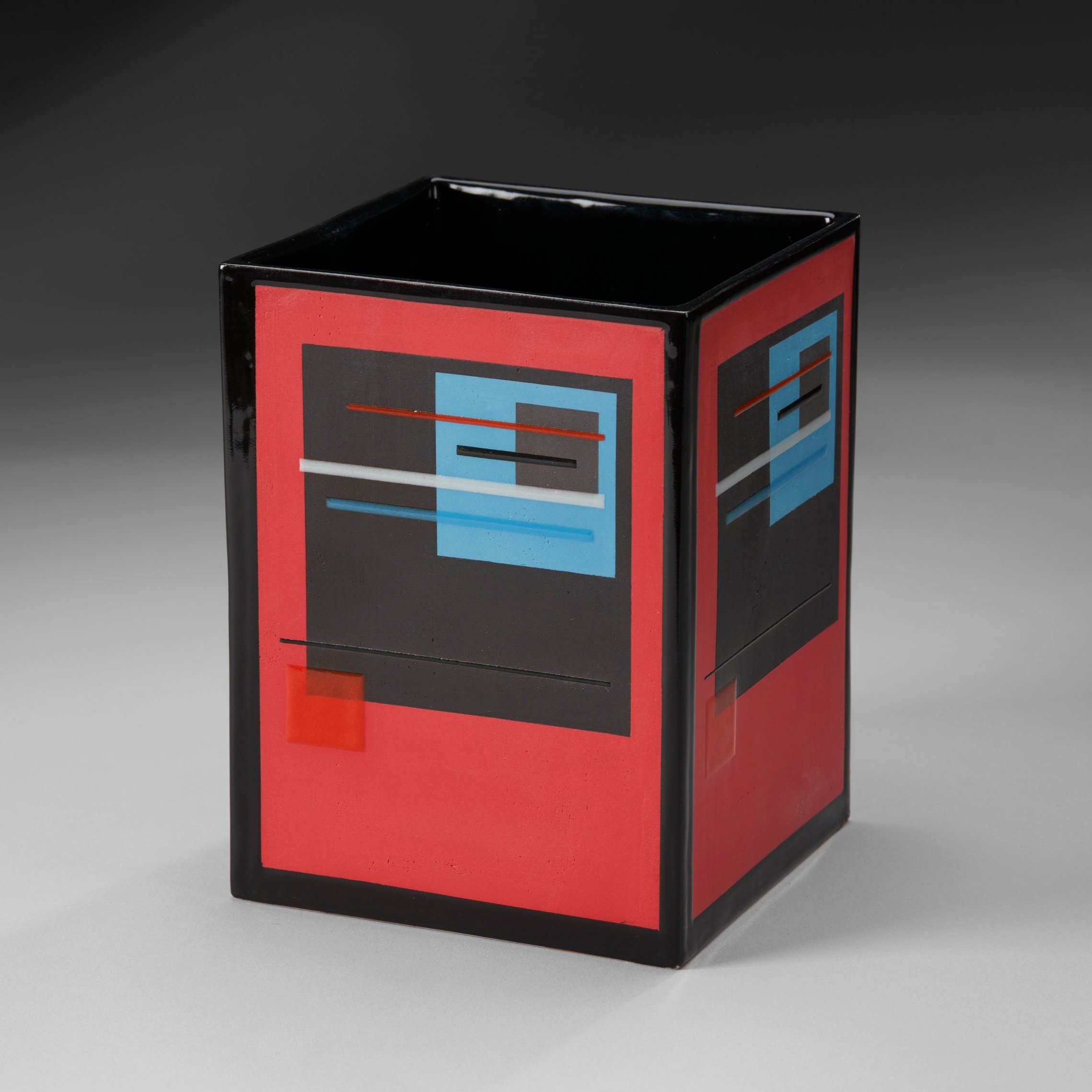
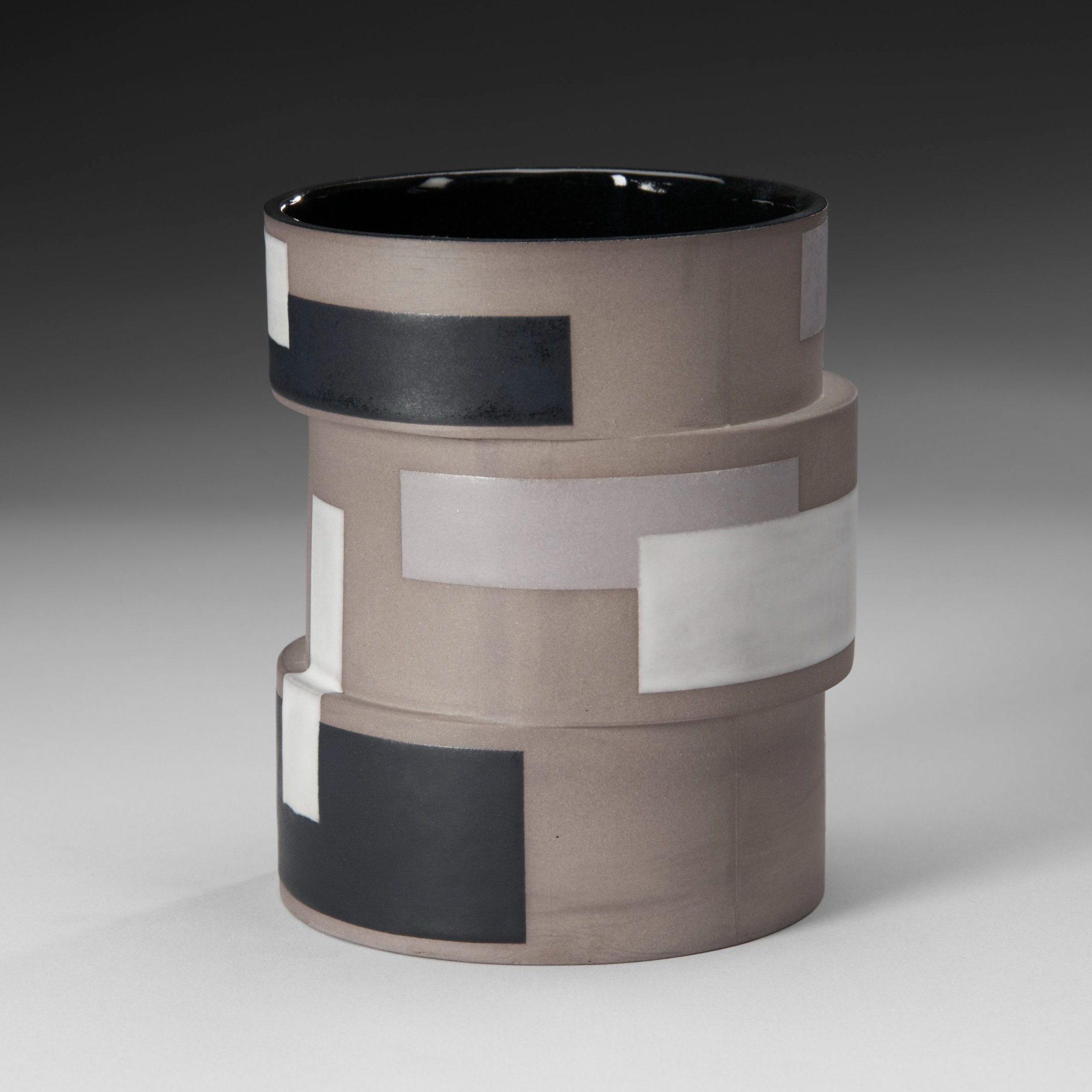
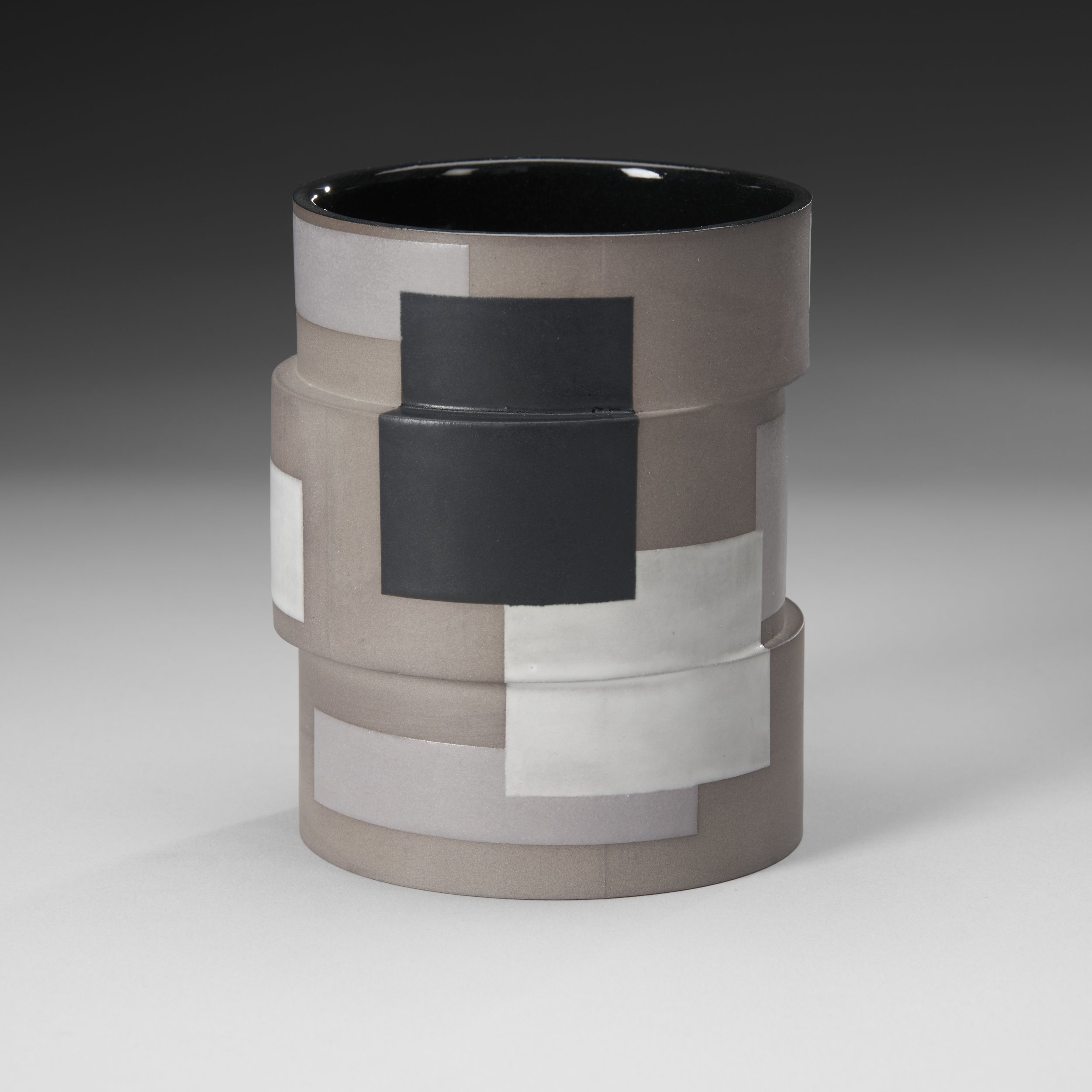
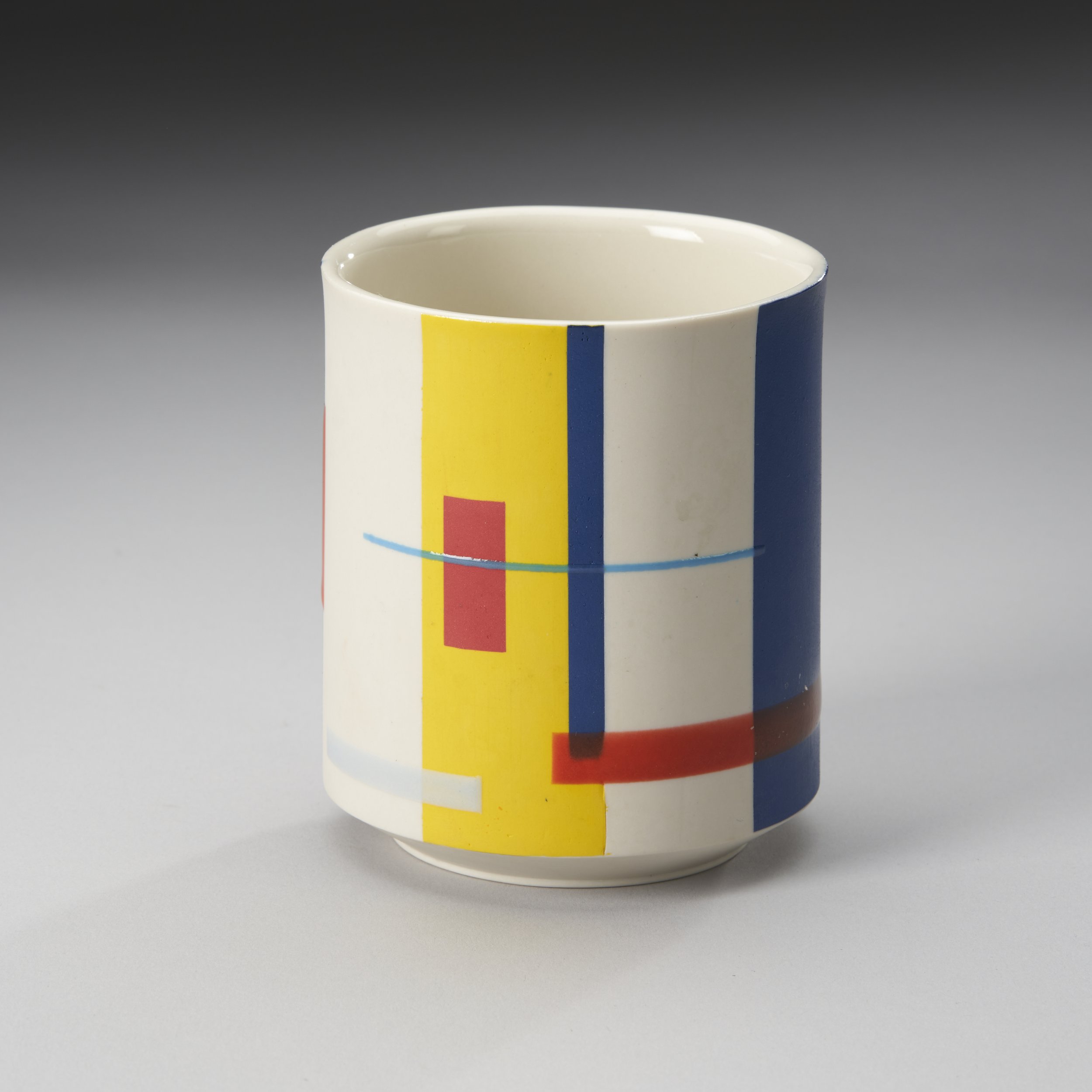
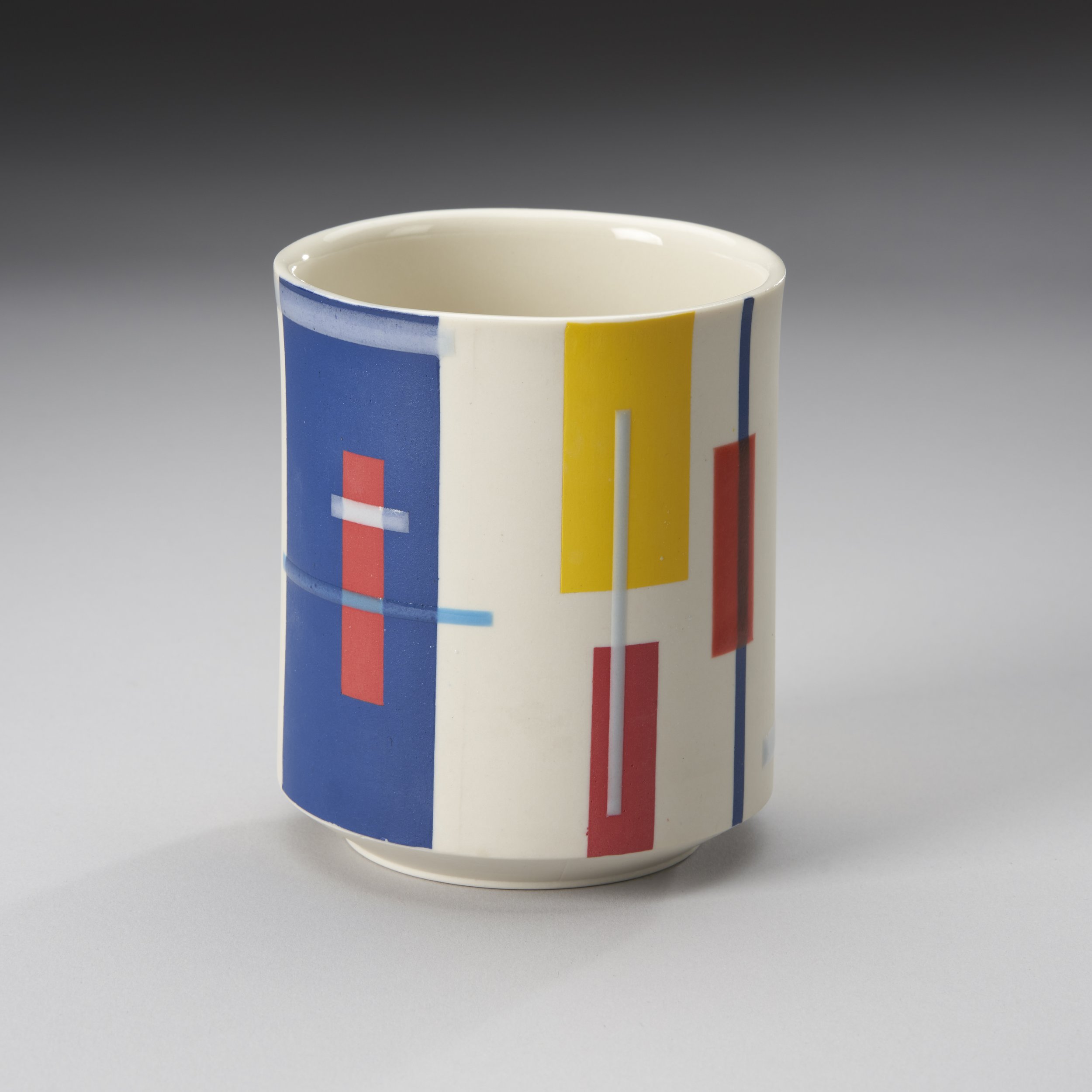
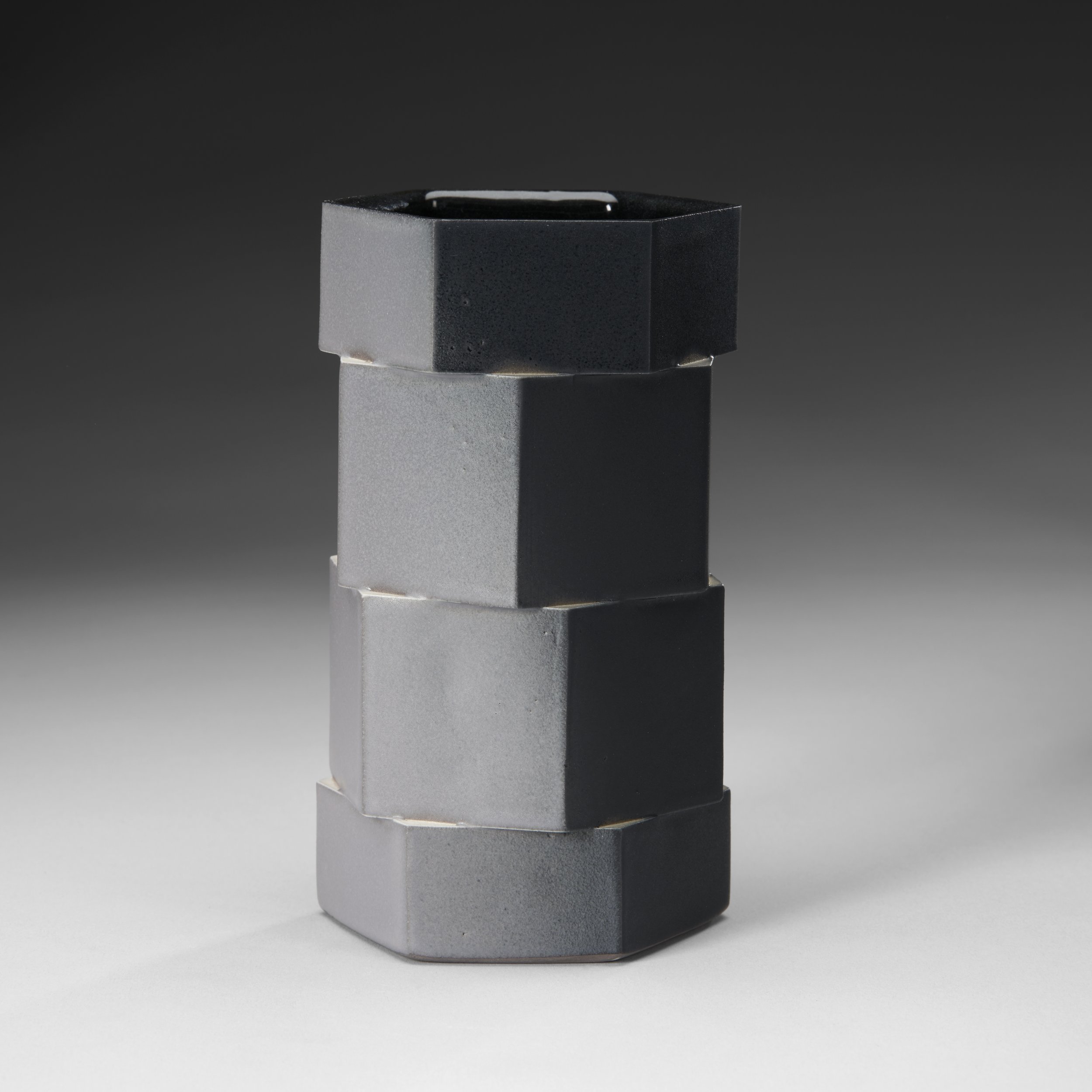
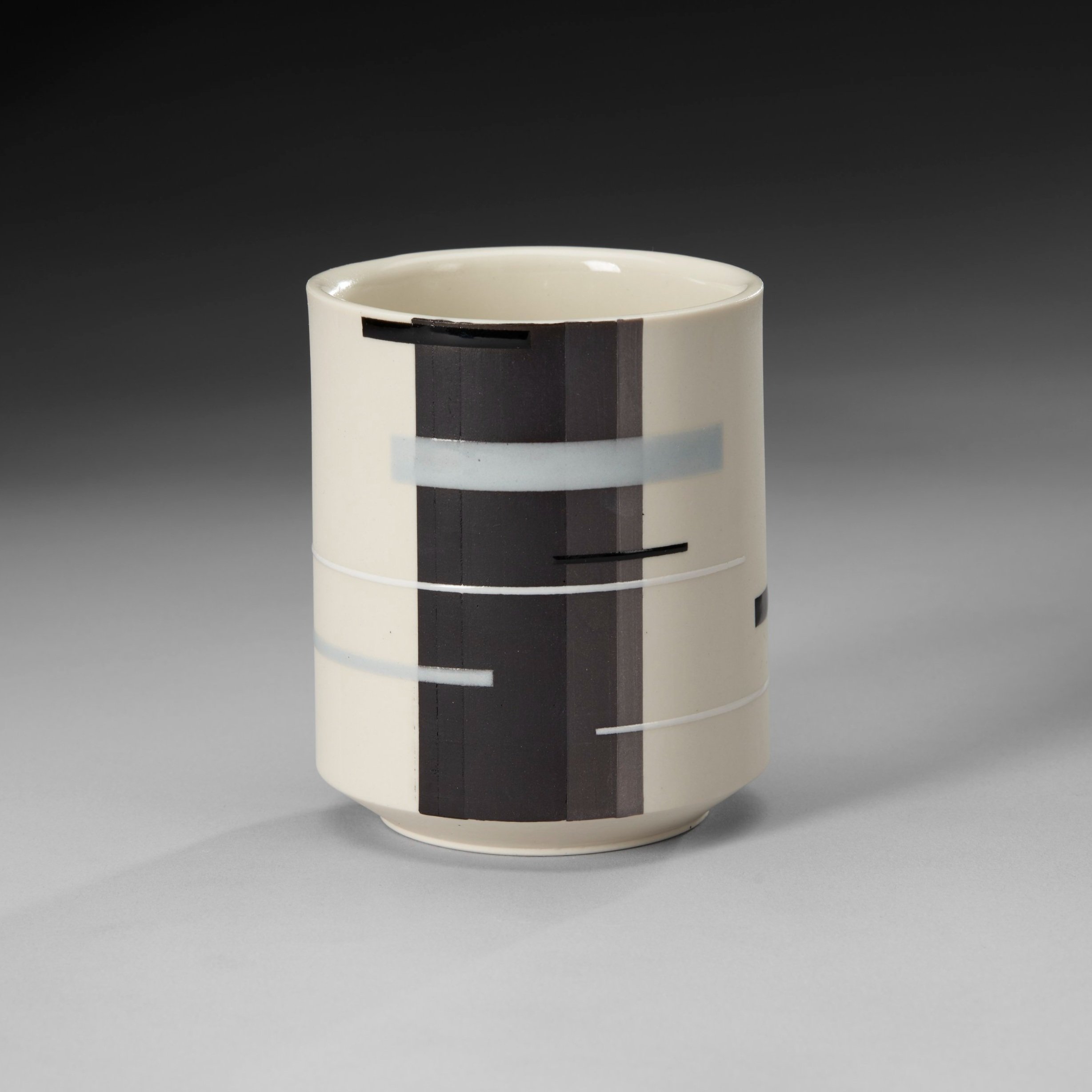
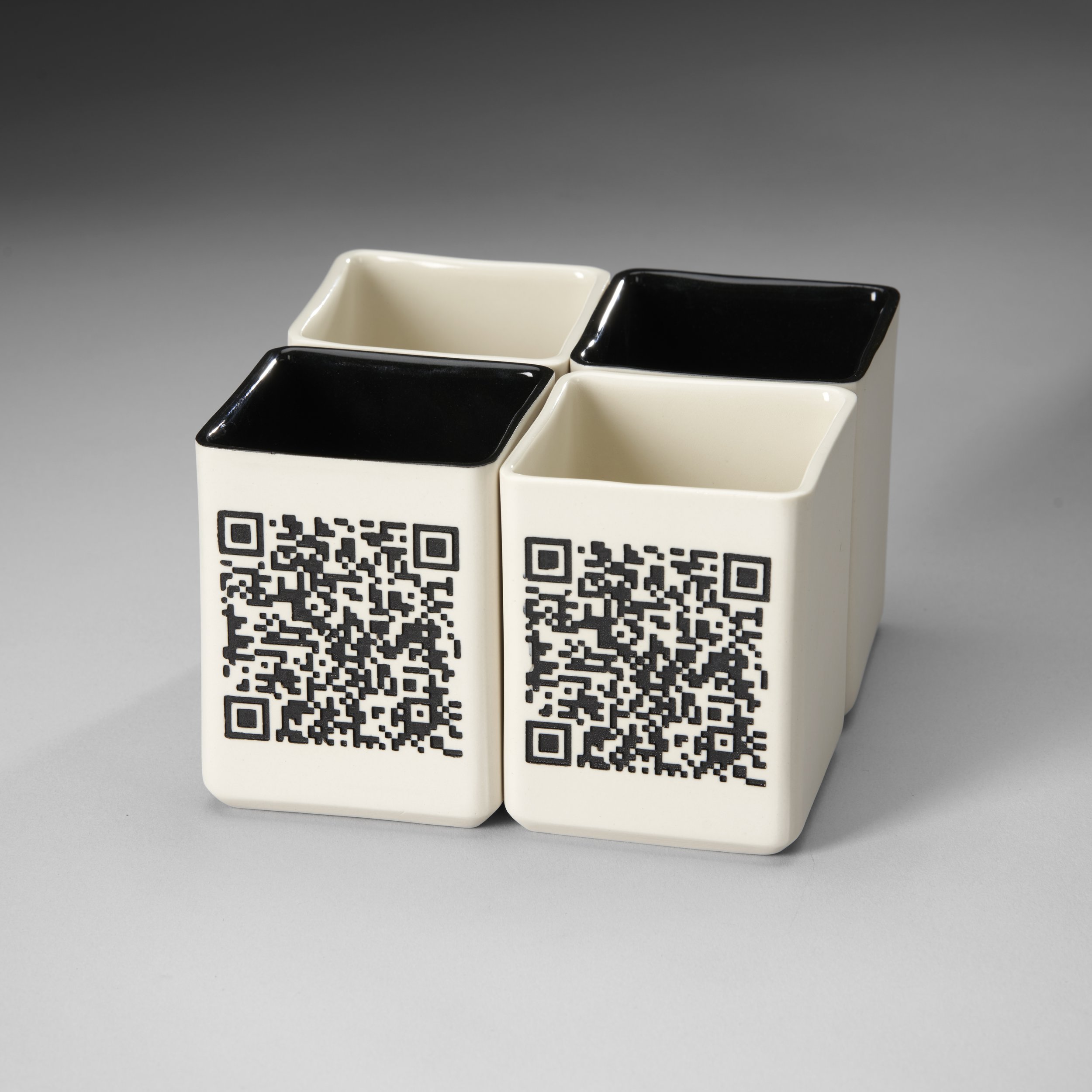
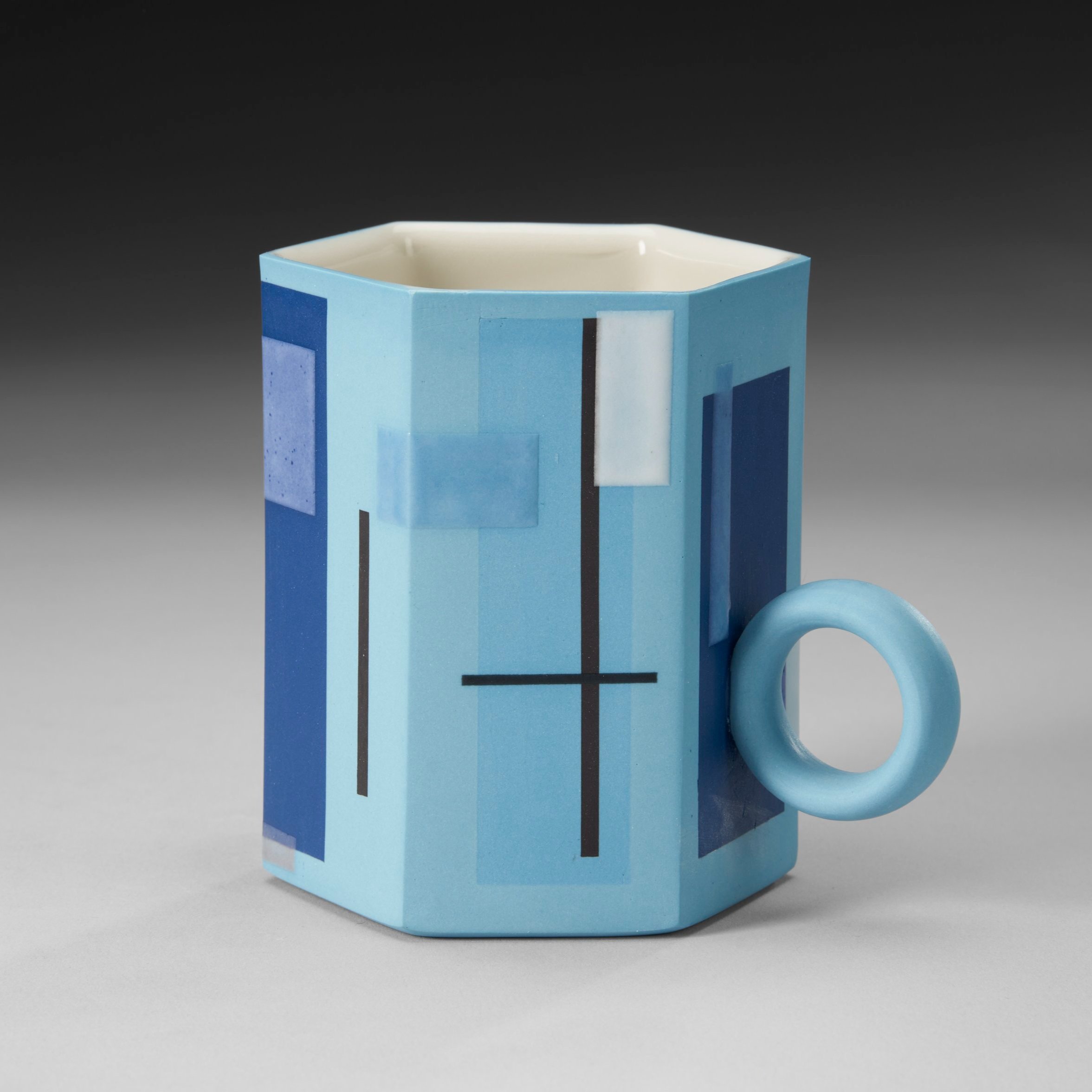
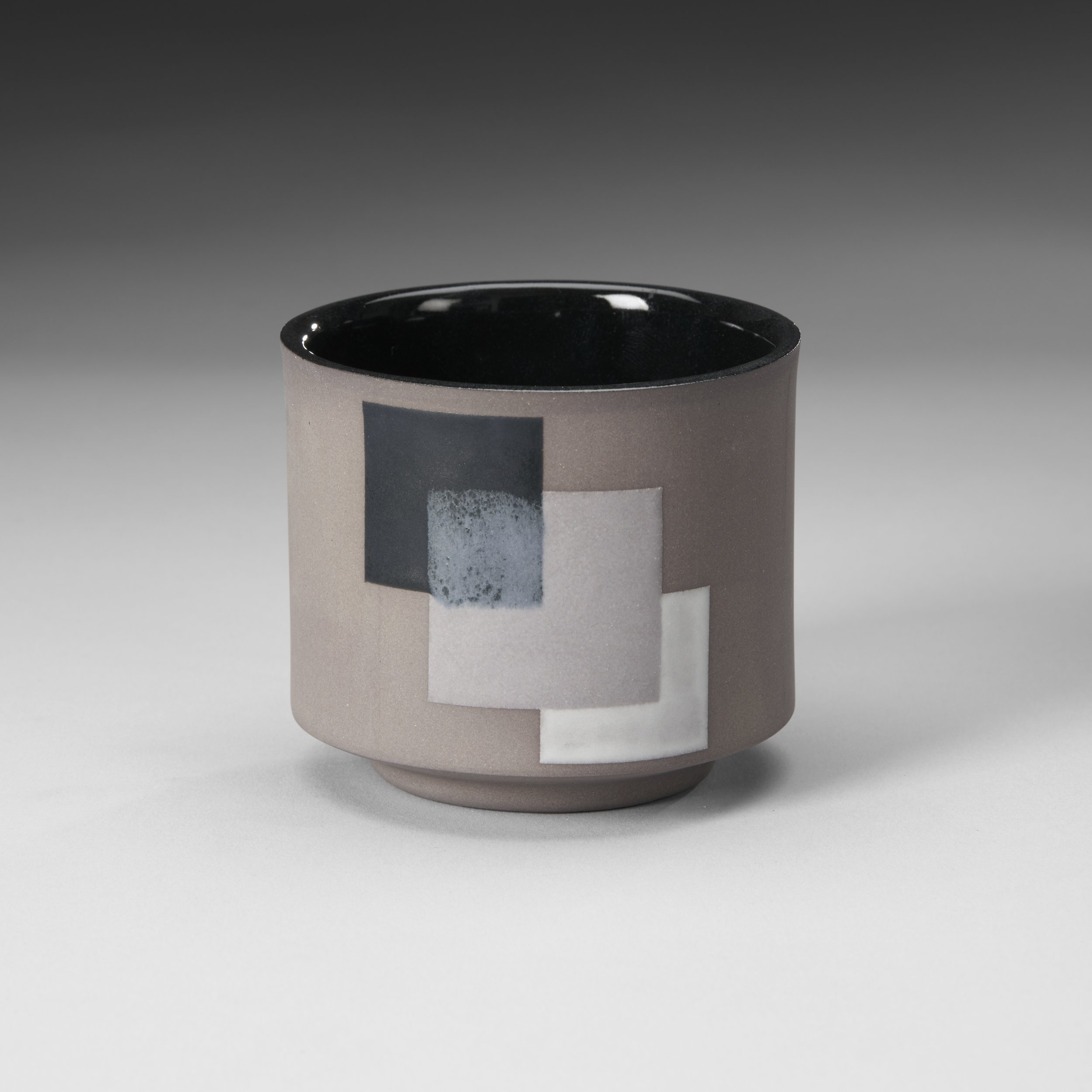
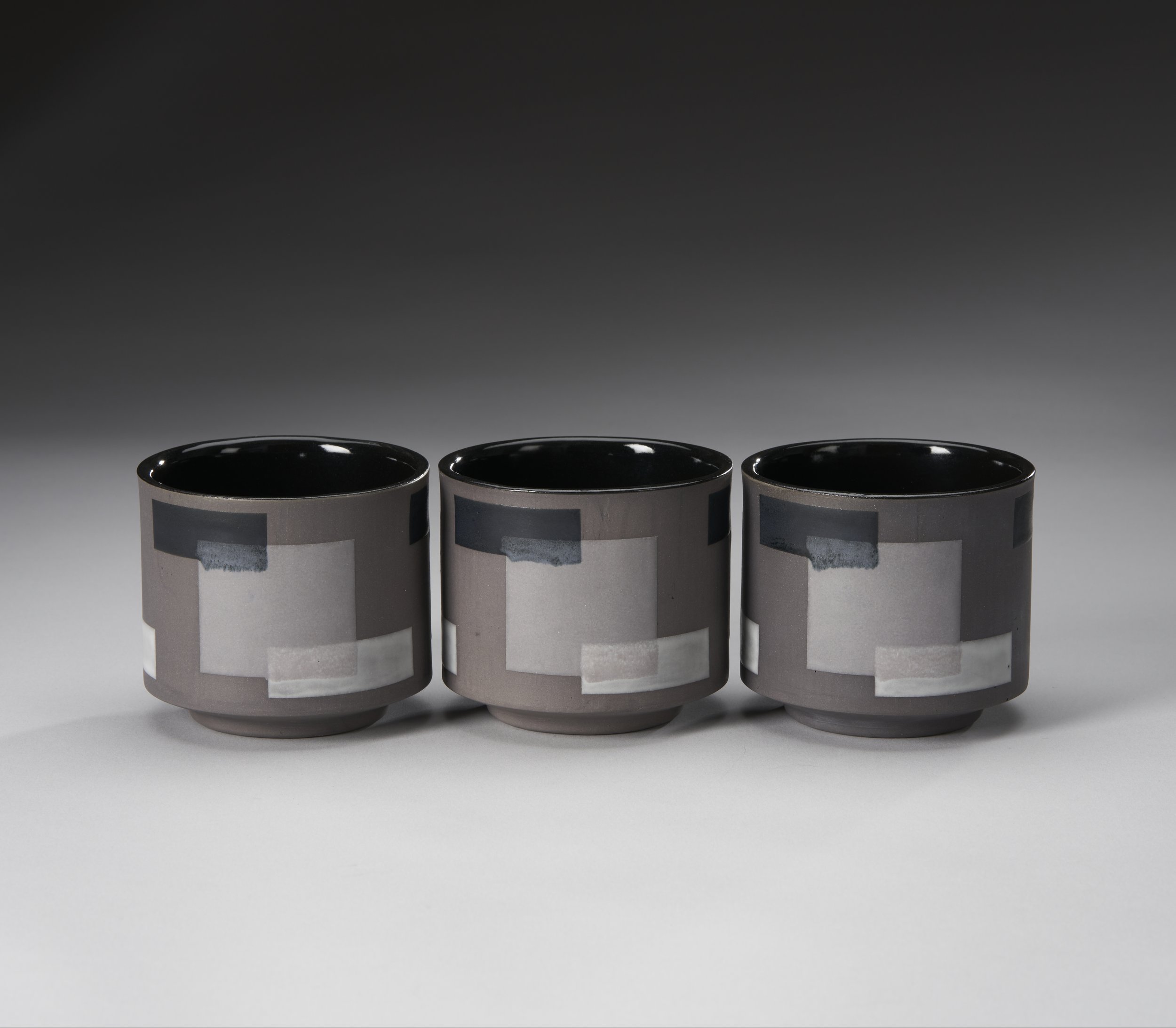
Realizing Refinement
I divided my 12-month fellowship into 3 “seasons” of professional development: Renovation, Studio Practice, and Refinement.
After completing my undergraduate degree at the Rochester Institute of Technology in May of 2023, I moved back home to Chicago. There I returned to the basement studio that my father and I had built while I was in high school. This space was equipped for making wheel-thrown pottery, however, the work I was striving to create was rooted in plaster mold-making and slip-casting. This process requires an entirely different set of tools and makes a particular type of mess that I would need to anticipate and accommodate. Therefore, before I could begin my artistic production, I needed to re-design my studio by implementing new work surfaces and equipment.
Thus began my first season, Renovation, which began in June of 2023, and came to a close in early August. I began at the hardware store, where I bought enough 2x4 lumber to build a new marble-top work bench. Marble provides a smooth and non-porous surface that is ideal for working with plaster. I also installed a ventilation pump to collect and extract airborne dust, which is very common in a ceramic studio, and can cause long-term health risks if not addressed. While the pump itself was easily acquired, the installation of PVC piping, plastic tubing, and copper grounding wire needed to make the system functional proved to be a week-long renovation challenge. Once this was completed, I had a brand new work bench accompanied by an overhead ventilation system that could carry plaster and ceramic dust outside to safely settle into the ground. While this new workstation was perfect for making my molds, I still needed an efficient way to dry them if they were to be functional. In a separate section of the basement studio, I constructed a drying rack using a wire shelving unit connected to two powerful box fans. Alongside this rack I installed a dehumidifier, which would expedite the process of drawing moisture out of my completed mold systems. Other equipment I added to the basement studio space during this time included a bandsaw, large basin slip mixer, vacuum pump, spray hood, and additional storage space. Even with all of this work completed, I was not yet ready to create my ceramic body of work.
To complete my season of Renovation, I acquired the most crucial piece of the proposal puzzle: the resin 3D printer. I outfitted a small empty closet into a [makeshift?] printing lab. The seclusion provided by the closet prevented sunlight from sneaking through windows, which could interfere with the UV-sensitive resin. With basement renovations complete and hope in my heart, I began printing components to manufacture my proposed master molds - I was immediately greeted with failure. This disruption began a trial-and-error process of failed prints, wasted material, and sickening frustration. One month, 15 digital test files, and about 100 rubber gloves later, I had finally dialed in my printing process. I was finally ready to begin what I had set out to do, and the season of Studio Practice commenced.
During my second season, I put my design skills and new equipment to the test. I began creating my molds using a multistep process that combined digitally created objects and hands-on studio techniques. First, I prototyped the ceramic object that I desired to create using clay or cardboard. Once I was satisfied with the appearance, scale, and proportions of this prototype, I created a digital model of it using Fusion 360, a CAD software. Then I designed a modular mold system around this digital object using the same technique. These mold components would ultimately become plaster, but first I brought them out of the digital, and into the physical world using my resin 3D printer. With this master mold component in hand, I cast flexible silicone around it, providing me with the negative of each component. Essentially, I was making a mold of the mold! Once each mold component had a corresponding silicone negative, I began pouring plaster into them, creating the final version of the 3D-printed master. The end result was an efficient way to replicate my plaster mold systems. While this process involved extensive work on the front end, it made mixing and pouring plaster less time-consuming and wasteful. Some of these initial mold systems made it all the way through this process from prototype to master mold, but were not as successful as I would have hoped. I took what I learned from those projects and applied it towards the final season of my grant period; Refinement.
The final season of my fellowship began in December of 2023, and was my focus throughout the rest of the grant period. I began by re-evaluating what I had already created, and taking notes on what accomplished my goals, versus what was simply unsuccessful. I adjusted my focus, spending time with a smaller number of mold systems, but, creating much more [effective?] work. I found that narrowing my production to only a few forms at a time allowed me to spend more energy perfecting the surface decoration that I had developed during my time of Studio Practice. This “less-is-more” approach encouraged me to lend a closer eye towards certain details that are crucial to a piece of fine studio ceramics: firing process, physical integrity, weight (both visually and physically), glaze application, historical context, and personal voice. I found that to achieve Refinement requires a certain amount of time spent with a given material, its production process, and the studio space that surrounds it all.
My experience over the last 12 months as a Windgate Fellow has given me a foundation for my career, as well as a window into the future. It has presented me with successes and challenges that are indicative of the artistic process. Along with the freedom to create, this opportunity has given me an introduction to the “real world”. I have learned how to manage my time, budget, and expectations, which are all very important factors to consider as I move forward in my career. This opportunity has introduced me to amazing people and presented me with more possibilities than I ever thought possible. It has allowed me to establish myself as an artist in the Chicago-land area. Now more than ever, I am confident in the work that I am creating and have established a body of work that I can truly call my own.
This project was supported by a Windgate-Lamar Fellowship Award administered by the Center for Craft.